|
 |
Rapid Prototyping/ Digitalization |
|
|
 |
 |
Models in the Production Process
A model is an image of reality, although the model does not have to represent all the properties of the desired prototype. Models used in product development are distinguished between shape, mathematical and technical models. Shape models are designated as bigger or smaller scaled images, so that only the needed properties of the object are shown. For example, an optimized Wooden model for a wind tunnel. Visual Models are understood from pictures. Technical models are data qualities from the digital registration of the product. For example a computer generated CAD model.
The application of models in the production process have been and are under investigation by the Chair. A result of the investigations is the .Process Step Generator.. This documents the differences in the Production processes of applicable Models. Another focus point of the research, lies in the study of shape with respect to physical models in the production process, and the application of 3D-CAD Data through the digitalization of real objects. This study could lead to the production of numerous publications and dissertations in these areas of interests.
Digitalization is the physical or optical registration of the outer surface geometry of physical models, including the Data editing required for the reconstruction of the Part/Object. This is attained through the drawing of curves and/or faces, or described by computer generated polygons, both on the foundation of digital points.
The application of physical models also offers the possibility of a better relationship with non-technical fields, in any case, even across department and company divisions. It is easier for people to relate to an actual physical model rather than a group of two dimensional drawings. However, the application of the prototyping process is also for the manufacturer, through which they can get feedback based upon the first hand experience of seeing the potential product in a form that resembles what they intend to produce.
Physical Models can be produced with different procedures and materials. One possibility is the use of rapid prototyping processes. The demands on a model are different, corresponding to the stage of the progress of the production process. From these grounds it is reasonable, independent from applicable material or technology, to arrange model definitions and to allocate the steps of the product development.
|
|
|
|
 |
Rapid-Prototyping |
|
|
 |
 |
Rapid-Prototyping-Procedures
Procedures: - STL (Stereo Lithography)
- SGC (Solid Ground Curling)
- SLS Selectives Laser Sintern
- 3DP (3D-Printing)
- FLM (Fused Layer Manufacturing)
- LLM (Layer Laminated Manufacturing)
Generative Manufacturing Processes
Generative manufacturing processes are used to create physical models of a part though a principle of forming. The part is not produced by a material removal principle like milling, Rather, the part is developed from the addition of material to a build piece from either a liquid or powder state to a solid state. The manufacturing results without the application of forms or tools. The technology of the generative manufacturing process is named Rapid Prototyping.
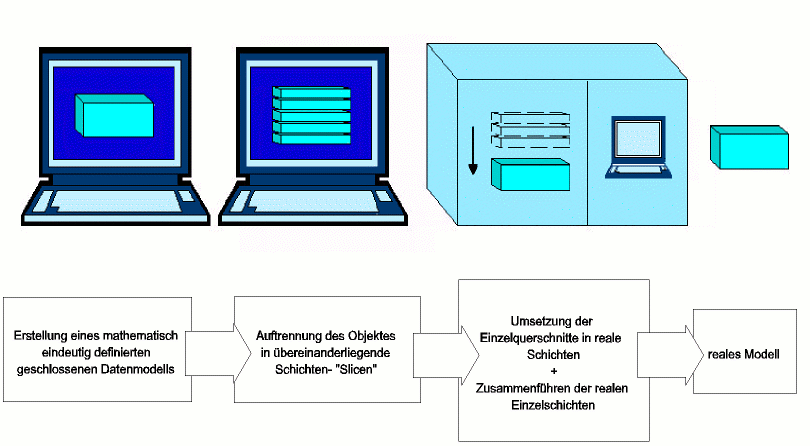 Picture: Illustration of the Manufacturing Process for RP-Models
All generative manufacturing processes have the same general manufacturing sequence:
1. Generation of the Manufacturing data - The finished model is a clear mathematical 3D-Data model that can be compiled with the help of a CAD program.
- The Object is in assembled from layers that are laid over each other corresponding to the process conditional layer thickness. This process is called slicing.
- For each particular contour of a layer the micro processor of the machine calculates the essential material assignment.
2. Manufacturing the part in the equipment The technological principle, the used material, as well as the resulting properties of the model are dependent upon the particular process.
Picture: Classification of the Rapid Prototyping Process
3. The model, in many cases, must be cleaned, coated for durability, or mechanically finished after it has been built.
|
|
|
RP Equipment of the Chair
LOM2030E
Z406
ThermoJet
Laminated Object Manufacturing (LOM) of the Firm Helisy Inc.
A laminated object manufacturing machine LOM2030E has been installed for the chair is since 1996. This LOM is the most known representative of the process group known as Layer Laminated Manufacturing (LLM). The idea of laminated object manufacturing (LOM) has been protected by the firm Helisys Inc.. The German distribution, the continuing development and attendance has been taken over by the firm RTV.
Three Dimensional Printer (3DP) of the firm Z-Corp
The RP system Z406 from the Z-Corporation employs a 3D-Print process (3D-Printer). The degree of detail is low, and the model can not be mechanically burdened without special Infiltration. The advantage of this process lies in the speed and the simple operation. With this System it is possible to manufacture multicolor models.
Solid Object Printer Termojet of the Firm 3D-Systems Inc.
The TermoJet, developed by the Firm 3D-Systems Inc., works as a 3D-Printer using the principle of fused layer manufacturing. It is was conceptualized and built for the fast and uncomplicated manufacture of concept models out of a hard wax like material called Termoplast and was designed to work as a 3D-Network Printer.
|
|
|
|
|
|
|